Fibrokompozyty cementowe mają już kilkudziesięcioletnią historię, znajdują wiele zastosowań i ciągle są doskonalone.
Betony modyfikowane włóknami stalowymi (drutobetony, włóknobetony, betony o zbrojeniu rozproszonym) funkcjonują na polskim rynku budowlanym od około 30 lat. Po pierwszym okresie pewnej nieufności projektantów i technologów betonu do tego nowego materiału znalazł on wiele zastosowań, z których najbardziej obecnie znane i rozpowszechnione to posadzki przemysłowe. Z uwagi na różnorodność kruszyw, włókien oraz dodatków i domieszek stosowanych do wykonania tego typu betonów coraz częściej nazywa się je fibrokompozytami cementowymi.
Wielkość ziaren kruszywa wpływa na rozkład włókien w fibrokompozycie cementowym. Stosowanie kruszyw grubych uniemożliwia prawidłowe jednorodne rozprowadzenie włókien w całej mieszance, a tym samym uzyskanie fibrokompozytu o zadowalających parametrach wytrzymałościowych. Włókna stalowe ulegają najlepszemu rozkładowi w matrycy wykonanej z kruszyw o uziarnieniu do 5 mm. Im większa zawartość w mieszance kruszywa grubego, tym mniejsza ilość włókien, jaką maksymalnie można modyfikować; według amerykańskich zaleceń zawartych w ACI 544 z 1993 r. betony zwykłe można modyfikować maksymalnie Vf = 2% w przypadku włókien o małej smukłości oraz Vf = 1% w przypadku włókien o dużej smukłości (Vf – objętościowa zawartość włókien w kompozycie cementowym). Możliwość otrzymania zapraw o wytrzymałości porównywalnej z wytrzymałością betonu zwykłego, a tym samym możliwość dozowania włókien bez obawy o brak równomiernego ich rozprowadzenia w mieszance spowodowała, że zaczęto interesować się zaprawami cementowymi jako materiałem do wykonania matrycy fibrokompozytu cementowego [4]. Fibrokompozyty cementowe wykonane na bazie matryc z zapraw cementowych służą m.in. do produkcji wielu elementów prefabrykowanych oraz torkretu.
W Polsce produkuje się np. cienkowarstwowe prefabrykaty ścian osłonowych [5] składające się z dwóch fibrokompozytowych warstw zewnętrznych o grubości 12−18 mm oraz wypełniającej warstwy termoizolacyjnej o grubości 160−230 mm. Omawiane elementy są bardzo lekkie, trwałe i co ważne tanie w produkcji dzięki prawie całkowitemu wyeliminowaniu pracochłonnego układania zbrojenia tradycyjnego w postaci prętów i strzemion. Przy zastosowaniu uproszczonej technologii produkcji i wytwarzaniu prefabrykatów o małych gabarytach (co pozwala na całkowicie ręczną produkcję) możliwe jest dalsze znaczne obniżenie kosztów produkcji tego typu elementów. W Kenii wytwarza się w warunkach uproszczonych cienkościenne prefabrykaty fibrokompozytowe o rdzeniu styropianowym stosowane do wznoszenia baraków mieszkalnych [1]. Prefabrykaty takie o wymiarach 1475 mm x 200 mm x 400 mm i masie 100 kg oraz sposób ich układania we wcześniej ustawionych słupach ściennych przedstawiono na rys. 1.


Rys. 1.Ścienny element fibrokompozytowy z rdzeniem styropianowym oraz sposób wznoszenia ściany zewnętrznej [1]
Ciekawym przykładem cienkościennych prefabrykatów fibrokompozytowych są szwedzkie elementy o przekroju trapezowym [8]. Pojedynczy prefabrykat ma długość 7 m, przekrój o wymiarach 1,8 m (dłuższy bok) x 1,8 m (wysokość) x 1,2 m (krótszy bok) i ma masę 6000 kg. Elementy te stosuje się do budowy portowych pirsów lub falochronów. Z sześciu prefabrykatów ustawionych pionowo obok siebie formuje się półkole stanowiące czoło pirsu. Wnętrze ustawionych prefabrykatów wypełnia się betonem zwykłym. Wykonane w ten sposób pirsy są bardzo trwałe, czego przykładem są falochrony na Wyspach Faroe. Pojedynczy element falochronu oraz układ elementów w czole pirsu przedstawiono na rys. 2.
Rys. 2.Widok cienkościennego elementu fibrokompozytowego do budowy pirsu oraz schemat układu sześciu elementów w czole falochronu [5, 8]
Technika torkretowania pozwala na wznoszenie całych cienkościennych konstrukcji z zapraw cementowych modyfikowanych włóknami. Na rys. 3 przedstawiono sposób wznoszenia cylindrycznego zbiornika na wodę za pomocą tej techniki. Możliwości uzyskania w ten sposób elementów o najbardziej nawet rozbudowanych kształtach są wręcz nieograniczone, czego przykładem może być chociażby fibrokompozytowy barak przedstawiony na rys. 4.
Rys. 3. Wznoszenie cylindrycznego zbiornika na wodę przy zastosowaniu techniki torkretowania [5, 8]
Rys. 4. Cienkościenne fibrokompozytowe pomieszczenie magazynowe [5, 8]
W przypadku zwykłego fibrokompozytu cementowego najpierw mieszamy w betoniarce składniki matrycy cementowej, a następnie do tej samej ciągle pracującej betoniarki dozujemy włókna stalowe. Ilość włókien stalowych podawana w trakcie mieszania składników matrycy cementowej jest ograniczona poprzez urabialność całej mieszanki. Włókna w znaczący sposób obniżają płynność mieszanki, a przy niekorzystnym układzie składników same włókna, zamiast zostać równomiernie rozprowadzone w całej objętości mieszanki, zaczynają się zbijać w tzw. jeże. Wraz ze wzrostem ilości włókien stalowych znajdujących się w matrycy cementowej wzrasta quasi-plastyczność fibrokompozytu cementowego i związane z nią specyficzne cechy wytrzymałościowe tego materiału, np. odporność na zarysowanie czy udarność. Według danych dostępnych w literaturze [2, 3] graniczną ilością włókien, którą można dozować w ten sposób do matrycy cementowej, jest 3% objętości całego zarobu.
W celu uzyskania fibrokompozytów cementowych o znacznie większej zawartości włókien stalowych niż przy tradycyjnym ich podawaniu należało zmienić sposób dozowania. Najprostszym rozwiązaniem wydawało się ułożenie włókien w przygotowanej formie, a następnie wypełnienie jej bardzo płynną mieszanką matrycy cementowej. Pomysł ten możliwy był do realizacji dopiero po wejściu na rynek budowlany wysoko sprawnych plastyfikatorów nowych generacji, które umożliwiły wykonanie odpowiednio ciekłej mieszanki matrycy cementowej. Pierwszy fibrokompozyt cementowy, w którym włókna zostały ułożone w formie, a następnie zalane samozagęszczającą się mieszanką drobnoziarnistej matrycy cementowej, wykonano w 1979 r. [2, 7]. Fibrokompozyty wykonywane w taki sposób nazywane są po angielsku SIFCON (Slurry Infiltrated Concrete). Dzięki zastosowaniu tej nowatorskiej metody dozowania włókien możliwe jest uzyskanie ich zawartości w matrycy od 4 do 27% (objętościowo). Ilość włókien, jaką jesteśmy w stanie umieścić w formie, zależy od ich kształtu, smukłości oraz sposobu wibrowania formy przy ich układaniu. Proces wykonywania elementu o dużej zawartości włókien stalowych z wykorzystaniem samozagęszczającej się zaprawy cementowej przedstawiono na fot. 1.
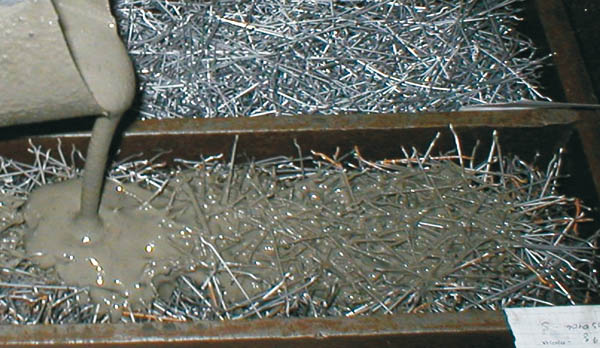
Fot. 1.Proces wykonywania elementu typu SIFCON (fot. autor)
Na wykresie przedstawiono zawartość włókien stalowych w fibrokompozytach cementowych o dużej zawartości włókien stalowych w zależności od smukłości zastosowanych włókien. Omawiane kompozyty betonowe wykonano w Laboratorium Techniki Budowlanej Politechniki Koszalińskiej, przy zastosowaniu włókien stalowych zakończonych haczykami o długości 50 i 60 mm.
Fibrokompozyty cementowe o dużej zawartości włókien stalowych cechuje o wiele większa od zwykłych fibrokompozytów cementowych quasi-plastyczność, a tym samym duża wytrzymałość na rozciąganie przy zginaniu oraz odporność na obciążenia dynamiczne i zmęczeniowe. Fibrokompozyty cementowe charakteryzują się też zwiększonym ugięciem w stosunku do betonu zwykłego, przy którym następuje ostateczne zniszczenie elementu. Oznacza to konieczność wydatkowania dużo większej energii do zniszczenia fibrokompozytu niż betonu zwykłego. Fibrokompozyty cementowe o dużej zawartości włókien stalowych (SIFCON) charakteryzują się jeszcze większym ugięciem niż zwykłe fibrokompozyty cementowe, przy którym następuje ostateczne zniszczenie elementu. Energia potrzebna do ostatecznego zniszczenia elementu typu SIFCON jest znacznie większa niż energia potrzebna do zniszczenia tego samego elementu wykonanego ze zwykłego fibrokompozytu.
W przypadku tradycyjnych fibrokompozytów cementowych, w których nie zastosowano żadnych specjalnych technik ukierunkowywania włókien, możemy przyjąć, że wszystkie włókna ułożone są jednorodnie w całej objętości matrycy i zorientowane w przypadkowy sposób we wszystkich kierunkach. Fibrokompozyty o dużej zawartości włókien stalowych mają w odróżnieniu od tradycyjnych fibrokompozytów z góry określony główny kierunek zorientowania włókien w betonowanym elemencie. Przy projektowaniu takiego elementu ważne jest, aby ściśle określić kierunek i rodzaj przyszłego obciążenia, jakie będzie na niego działać. W zależności od kierunku działania obciążenia w stosunku do kierunku ułożenia włókien w betonowanym elemencie charakteryzuje się on różnymi parametrami wytrzymałościowymi.
Wraz ze wzrostem ilości włókien stalowych znajdujących się w matrycy cementowej wzrasta quasi-plastyczność fibrokompozytu i związane z nią specyficzne cechy wytrzymałościowe tego materiału. Główną cechą odróżniającą fibrokompozyty cementowe o dużej zawartości włókien stalowych od zwykłych fibrokompozytów są znacznie większe odkształcenia towarzyszące procesowi zniszczenia próbki podczas ściskania [3]. Po osiągnięciu maksymalnej siły ściskającej próbka wykonana z fibrokompozytu cementowego o dużej zawartości włókien stalowych ciągle stanowi jedną całość i może przenosić pewne obciążenia – rys. 5.
Rys. 5.Cylindryczna próbka wykonana z kompozytu cementowego (φ = 150 mm, h = 500 mm) o dużej zawartości włókien stalowych po badaniu na ściskanie [3, 8]. Próbka mimo wyczerpania już maksymalnej nośności dalej stanowi jedną całość i jest w stanie przenosić pewne obciążenia
Zjawisko to jest bardzo ważne ze względu na tzw. proces bezpiecznego przebiegu katastrofy budowlanej. Na bezpieczny przebieg katastrofy budowlanej kładzie się nacisk w rejonach szczególnie narażonych na trzęsienia ziemi oraz na przykład w przypadku budowli o podwyższonym ryzyku eksplozji. Zdolność do dużych odkształceń przed ostatecznym zniszczeniem, a tym samym pochłanianie znacznych ilości energii w trakcie procesu niszczenia są bardzo ważnymi zaletami materiału konstrukcyjnego.
Głównym czynnikiem, który decyduje o poprawnym wykonaniu fibrokompozytu cementowego o dużej zawartości włókien stalowych, jest samozagęszczająca się mieszanka drobnoziarnistej matrycy cementowej. Wykonujemy ja na bazie piasku o uziarnieniu do 0,5 mm znacznie większej niż w betonach zwykłych ilości cementu, dodatków pucolanowych, takich jak pyły krzemionkowe czy popioły lotne, oraz przy zachowaniu W/C od 0,25 do 0,45 [3, 6]. Na fot. 2 przedstawiono przykładowy rozpływ pierścienia wykonanego z cementowej zaprawy samozagęszczającej się.
Fot. 2.Samozagęszczająca się zaprawa cementowa
Dużą płynność i brak wycieku wody uzyskuje się poprzez domieszkę superplastyfikatora, dodatek pyłów krzemionkowych oraz mączki bazaltowej. Ilość włókien, jaką jesteśmy w stanie umieścić w formie, zależy od ich kształtu, smukłości oraz sposobu wibrowania formy przy ich układaniu. Przykładową recepturę zaprawy samozagęszczającej się przedstawiono w tabeli.
Składnik
|
Ilość
|
Wskaźniki
|
kg/m3
|
W/C
|
W/K
|
Cement
|
540
|
0,4
|
1,0
|
Woda
|
240
|
Kruszywo
|
540
|
Mączka bazaltowa
|
60
|
Pyły krzemionkowe
|
60
|
Super-
plastyfikator
|
18
|
Skład przykładowej samozagęszczającej się zaprawy cementowej
Fibrokompozyty cementowe modyfikowane dużą ilością włókien stalowych nie są jeszcze materiałem powszechnie stosowanym w budownictwie. Głównymi czynnikami hamującymi ich szerokie wkraczanie do praktyki budowlanej jest dość trudna technologia wykonania, związana z precyzyjnym dozowaniem i mieszaniem składników, oraz cena wynikająca z konieczności stosowania dużej ilości włókien stalowych, cementu oraz drogich dodatków i domieszek. W pewnych wybranych przypadkach trudności związane z wykonaniem kompozytów typu SIFCON w pełni się opłacają. Dobrym przykładem są tutaj specjalistyczne budowle do magazynowania materiałów wybuchowych. Duże zainteresowanie tego typu betonami występuje również w krajach szczególnie narażonych na trzęsienia ziemi, gdzie „bezpieczny” sposób niszczenia takich elementów fibrokompozytowych pozwala myśleć o wznoszeniu budynków zapewniających bezpieczną ewakuację mieszkańców tuż po zaistniałym kataklizmie.
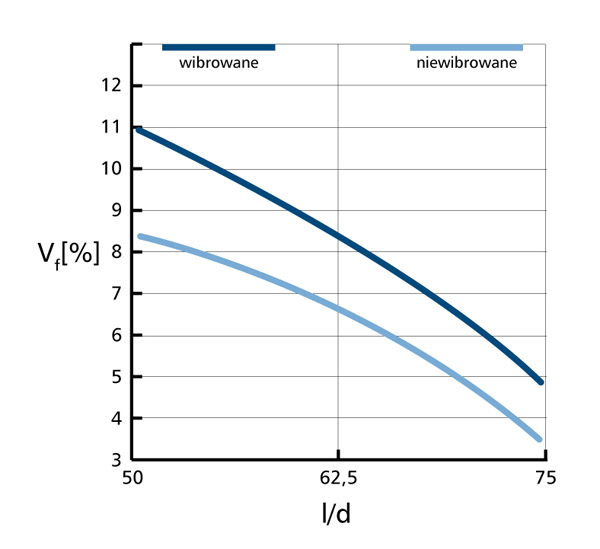
Przykładowa zawartość włókien stalowych w fibrokompozycie o dużej zawartości włókien w zależności od ich smukłości i wibrowania (podczas układania w formie)
Najnowszym osiągnięciem w dziedzinie fibrokompozytów cementowych o dużej zawartości włókien stalowych jest technologia SIMCON (Slurry Infiltrated Mat Concrete). Jest to system, w którym funkcję rozproszonych włókien pełni gęsta mata wykonana z włókien stalowych. Mata wykonana jest z włókien o średnicy od 0,25 do 0,50 mm i długości 241 mm. Mata produkowana na razie w skali laboratoryjnej jest zwijana w rolki, które można łatwo transportować, a na miejscu budowy dowolnie ciąć, formować i układać. Tak przygotowane „zbrojenie” wypełnia się poprzez technikę iniekcji drobnoziarnistą samozagęszczającą się zaprawą cementową. Prace nad SIMCON prowadzone są pod naukową opieką profesora Jamesa Romualdi twórcy pierwszej teorii fibrobetonu.
dr inż. Jacek Katzer
Politechnika Koszalińska
Bibliografia
1. S. DeBoer et al., Low-cost housing in Kenia, Delft University of Technology, September 2004.
2. Z. Jamrozy, Drutobeton, Wydawnictwo Politechniki Krakowskiej, Kraków 1985.
3. C.D. Johnston, Fiber-reinforced cement and concretes, Gordon and Breach Science Publisher, Amsterdam 2001.
4. J. Katzer, Properties of Precast SFRCC Beams Under Harmonic Load, Science and Engineering of Composite Materials, Vol.15, No. 2, 2008, pp. 107–120.
5. J. Katzer, Z. Piątek, Aplikacje budowlane betonów modyfikowanych włóknami stalowymi, XVIII Konferencja Naukowo-Techniczna „Beton i prefabrykacja Jadwisin 2002”, 10–12 kwietnia 2002, Popowo.
6. N. Krustulovic-Opara, H. Toutanji, Infrastructural repair and retrofit with HPFRCCs, Proceedings of the Second International RILEM Workshop, 1995.
7. D.R. Lankard, Preparation, Properties and Applications of Cement-based Composites Containing 5 to 20 Percent Steel Fiber, Steel Fiber Concrete US-Sweden joint seminar, Stockholm 3–5 June 1985.
8. S.P. Shah, A. Skarendahl, Steel fiber concrete, Elsevier Applied Science Publishers, London and New York 1985.