Konstruktorzy nie ustają w wysiłkach, aby takie właśnie były maszyny budowlane.
Ośmiu z dziesięciu nabywców maszyn budowlanych przy wyborze konkretnej marki i modelu bierze pod uwagę wydajność i oszczędność eksploatacji. Trudno się temu dziwić, któż bowiem nie chciałby mieć maszyny niewymagającej wielu nakładów finansowych i jednocześnie wydajnej. Jednak czy takie maszyny w ogóle istnieją? Inżynierowie i naukowcy nie ustają w dążeniach, by dokonać z pozoru niemożliwego, to znaczy znaleźć złoty środek pozwalający budować maszyny wydajne, oszczędne, komfortowe i bezpieczne.
Aby stworzyć maszynę mającą ograniczony apetyt na paliwo, nie wystarczy zamontowanie w niej oszczędnego silnika. To byłoby zbyt proste. Konieczne jest zastosowanie kompleksowych rozwiązań dotyczących całej konstrukcji. Główne możliwości leżą w ograniczeniu masy, która musi być przemieszczana przez maszynę do robót ziemnych podczas każdego z cykli roboczych. I nie chodzi tu bynajmniej o urobek. Maszyna powinna dać sobie radę z coraz większą masą ładunku. Nie zapominajmy jednak, że każda koparka podczas normalnej pracy musi się zmagać dodatkowo z tonami stali użytej do jej budowy. Rozwiązanie problemu nasuwa się samo. Niezbędna jest „kuracja odchudzająca”. Zmniejszenie masy maszyny nie jest prostym zabiegiem, nie może bowiem odbywać się kosztem ograniczenia stabilności i trwałości całej konstrukcji. Redukując masę własną maszyn, konstruktorzy zrezygnowali co prawda z niektórych elementów konstrukcyjnych, ale jednocześnie zadbali o wzmocnienie punktów podlegającym szczególnym obciążeniom.

Fot. 1. Dzisiejsze maszyny napędzane są nowoczesnymi silnikami imponującymi wysokimi osiągami i ograniczonym zużyciem paliwa
Praca tysięcy inżynierów centrów badawczo-rozwojowych rozsianych po całym świecie nad ulepszeniem systemów napędowych wymaga olbrzymich nakładów finansowych, jest mozolna, ale przynosi pozytywne rezultaty. Układy napędowe maszyn nowej generacji są coraz efektywniejsze, ekonomiczne w eksploatacji, nie obciążają przy tym nadmiernie środowiska naturalnego. Niżej podpisany miał swego czasu możliwość odwiedzenia szwajcarskiego Arbon, gdzie opracowywane są konstrukcje silników Fiat Power Train (FPT). Może nie wszyscy pamiętają, że to właśnie Fiat dopracował przełomową technologię Common Rail na tyle, by mogła ona zostać wdrożona do seryjnej produkcji. Fiat przejął założenia technologiczne od szwajcarskiego instytutu badawczego ETH Zürich, który zajmował się technologią Common Rail w latach 1976–1992, ale tylko ściśle teoretycznie. Silnika wykonanego w tej technologii Szwajcarzy nie zastosowali bowiem w żadnym pojeździe.
W nowoczesnych jednostkach napędowych wykorzystujących system Common Rail zamiast sekwencyjnej pompy paliwa stosowana jest pompa wysokociśnieniowa tłocząca paliwo do akumulatora zasilającego (zw. również listwą lub szyną) wspólnego dla wszystkich cylindrów. Ciśnienie utrzymujące się w tym przewodzie wynosi ok. 1350 barów, niezależnie od obciążenia silnika ani od jego prędkości obrotowej. Z akumulatora zasilającego paliwo podawane jest do sterowanych elektronicznie wtryskiwaczy, a stąd trafia bezpośrednio do komory spalania. Dzięki zastosowaniu wtryskiwaczy sterowanych elektronicznie możliwe jest dowolne kształtowanie czasu wtrysku, jego długości oraz dawki paliwa zależnie od wielu czynników, na przykład obciążenia silnika. Daje to również możliwość podziału wtrysku paliwa na trzy etapy, na które składają się: wtrysk pilotowy, właściwy oraz dawka dopalająca. Rozwiązanie to umożliwia lepsze spalanie paliwa, a dzięki temu zmniejszenie jego zużycia. W porównaniu z osiągami silników z wtryskiem mechanicznym oszczędności w tym zakresie sięgać mogą nawet do 35%. Kolejnymi zaletami systemu Common Rail jest ograniczenie emisji spalin, hałasu emitowanego przez jednostkę napędową oraz uzyskanie wysokich parametrów pracy. Obecnie stosowany system Common Rail drugiej generacji charakteryzuje się ciś-nieniem wtrysku rzędu 1600 barów oraz większą liczbą – nawet do siedmiu – faz wtrysku. Użytkownicy maszyn napędzanych silnikami wykonanymi w tej technologii muszą tankować paliwo najwyższej jakości. Zaopatrywanie się w olej napędowy co prawda tańszy, ale z niepewnego źródła to pozorna oszczędność. Paliwo o złych parametrach doprowadzić może bowiem do nieodwracalnego zniszczenia wtryskiwaczy pracujących pod wielkim ciśnieniem. Ich naprawa wiąże się z koniecznością długiego wyłączenia maszyny z normalnej eksploatacji i poniesieniem wysokich kosztów części i robocizny.
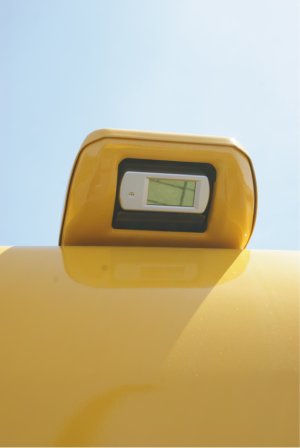
Fot. 2. Kamera montowana obligatoryjnie w maszynach o dużych gabarytach podnosi bezpieczeństwo pracy
Producenci ładowarek kołowych starają się czynić oszczędności eksploatacyjne dzięki usprawnianiu napędu hydrostatycznego. Konstruktorom udało się zintegrowanie komponentów w jednej osi. Maszyna funkcjonować może bez mechanicznej zmiany biegów, koła napędzane są bezpośrednio przez wolnoobrotowy silnik hydrauliczny. Zaawansowane układy elektroniczne zapewniają znakomite właściwości jezdne i pozwalają optymalnie wykorzystać moc silnika Diesla. Ma to olbrzymi wpływ na zmniejszenie zużycia paliwa.
Konstruktorzy ładowarek kołowych dążący do zwiększenia ich efektywności również starają się zredukować ich ciężar roboczy. W tym celu zmieniają rozmieszczenie niektórych podzespołów. Chłodnice przenoszone są za kabinę. Silnik umieszczony w tylnej części nadwozia umożliwia zmniejszenie ciężaru właściwej przeciwwagi, a tym samym masy całkowitej maszyny. Przykładowo 20-tonową ładowarkę udaje się w ten sposób „odchudzić” nawet o 900 kg bez ograniczeń w zakresie stabilności i wytrzymałości konstrukcji. Przekłada się to bezpośrednio na zmniejszenie zużycia paliwa podczas każdego cyklu roboczego. Jednocześnie zwiększyć można obciążenia, jakim może być poddawana maszyna, a tym samym żywotność elementów układu roboczego i całej konstrukcji nadwozia. Rozważając zakup nowej maszyny, należy zatem brać pod uwagę nie tylko jej ciężar roboczy.
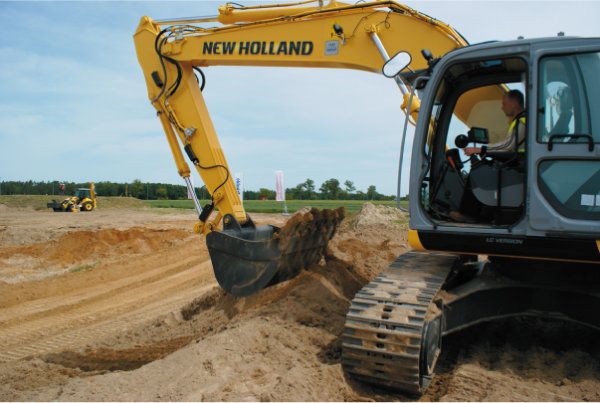
Fot. 3. Nowej generacji koparki mimo tradycyjnej konstrukcji są wydajniejsze i tańsze w eksploatacji
Maszyny nowej generacji mogą przemieszczać nawet do 15% więcej urobku w przeliczeniu na litr zużytego paliwa. Parametry te udało się osiągnąć nie tylko dzięki optymalizacji układu napędowego oraz zmniejszenia ciężaru roboczego. Analizując sprawność osiąganą przez dzisiejsze maszyny budowlane, których konstrukcję oparto na silniku spalinowym, pompach hydraulicznych i zasilanym przez nie osprzęcie, zauważyć należy, że energia generowana przez jednostkę napędową wykorzystywana jest w stopniu dalece niezadowalającym. Przeważająca jej część jest bowiem tracona, uciekając do atmosfery w postaci energii cieplnej. To właśnie w ograniczeniu tych strat upatrywać należy głównych możliwości oszczędniejszej eksploatacji maszyn. Można ją osiągnąć także dzięki optymalizacji rozwiązań stosowanych obecnie. Pojawiły się już koparki gąsienicowe, które mimo zastosowania wyłącznie klasycznych rozwiązań konstrukcyjnych w porównaniu z maszynami poprzedniej generacji są w stanie przemieścić o ok. 15% więcej urobku na każdy zużyty litr oleju napędowego. Efekt ten osiągnięto głównie dzięki zoptymalizowaniu konstrukcji układu hydraulicznego poprzez ograniczenie strat spowodowanych spadkami ciśnienia. Stanowią one specyfikę wszystkich układów hydraulicznych, dochodzi do nich na wszystkich przewężeniach poprzecznych, obojętnie czy maszyna pracuje pod pełnym obciążeniem, czy też na biegu jałowym. Aby ograniczyć straty, niezbędne okazało się kompleksowe przekonstruowanie systemu hydraulicznego w zakresie sterowania zaworami, połączeń przewodów i wszystkich elementów mających kontakt z cieczą hydrauliczną. Pozwala to na oszczędności eksploatacyjne w zakresie zużycia paliwa nawet o 10% w porównaniu z maszynami poprzedniej generacji. Co istotniejsze, odbywa się to przy jednoczesnym podniesieniu o 15% osiągów maszyny. Daje to również oszczędności dzięki skróceniu czasu wykonywania poszczególnych cykli roboczych.
Efektywność eksploatacji maszyn podnosi komfort pracy operatora. Nowoczesne koparki wyposażone są w przestronne kabiny zapewniające doskonałą widoczność na cały obszar roboczy. Manipulatory umieszczane są na specjalnej konsoli zintegrowanej z fotelem operatora. W ten sposób zachowana zostaje optymalna pozycja pracy, nawet gdy fotel musi być przestawiany dla różnych operatorów. Konstrukcja kabiny pozwala na zmniejszenie jej wagi przy jednoczesnym zachowaniu pełnego zakresu bezpieczeństwa ROPS/FOPS. Maszyny do robót ziemnych nowej generacji wyposażone są w system kamer pozwalający operatorowi śledzić pole pracy za maszyną. Niektórzy z producentów decydują się na wyposażenie systemu w osobny, obsługujący tylko kamery, duży monitor LCD. Dzięki temu operator może stale śledzić pole pracy za maszyną i nie odbywa się to kosztem braku wskazań z systemu monitorującego pracę podstawowych podzespołów i układów. Umożliwia to lepszą ocenę zagrożeń pojawiających się podczas pracy i szybszą na nie reakcję. Widoczność z kabiny poprawia również zmniejszenie gabarytów maszyn. Nie dzieje się to kosztem ograniczenia ich wydajności czy stabilności. Kompaktowa budowa pozwala nie tylko na ograniczenie zużycia paliwa, ale także poszerza zakres zastosowań maszyn. Mogą one wykonywać zadania także w miejscach o ograniczonej przestrzeni.
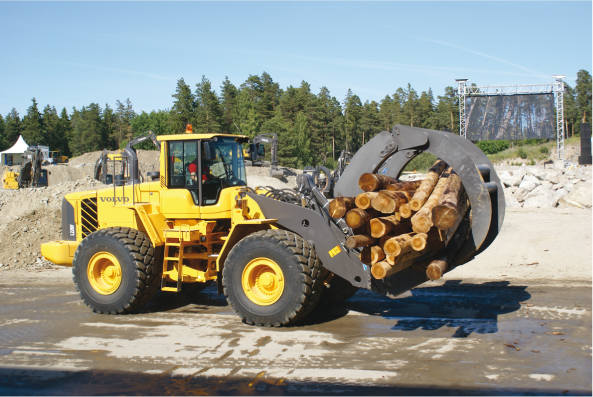
Fot. 4. Konstruktorzy ładowarek starają się maksymalnie „odchudzić” swoje maszyny
Niezwykle istotnym czynnikiem wpływającym na zwiększenie bezpieczeństwa pracy na placu budowy jest ograniczenie hałasu emitowanego przez maszyny. Dzięki temu podnosi się słyszalność komend wydawanych przez kierującego pracami i sygnałów ostrzegawczych. Nie można zapominać o negatywnym wpływie hałasu na samopoczucie oraz ogólny stan zdrowia operatora i osób pracujących w sąsiedztwie maszyny. Nadmierny hałas powoduje zmęczenie kierującego maszyną, a tym samym zmniejsza stopień efektywności jego pracy. Konstruktorzy New Holland mają na tym polu znaczące osiągnięcia, są już wdrożone do seryjnej produkcji 25-tonowe koparki (z systemem iNDr) emitujące hałas porównywalny z wytwarzanym przez silnik wysokoprężny większego samochodu osobowego.
Zdaniem wielu ekspertów przyszłość w zakresie napędu maszyn budowlanych – przynajmniej ładowarek kołowych – należeć może do układu hybrydowego. Zakładać przy tym należy, że rosnąć będą ceny ropy naftowej, spadać zaś koszt wytwarzania specjalnych akumulatorów niezbędnych w tej technologii. Pierwszy w pełni funkcjonalny napęd hybrydowy w maszynie budowlanej zaprezentowała szerszej publiczności już w 2006 r. podczas targów Intermat japońska firma New Energy Development Organization (NEDO). W jej ślady szybko poszli niemal wszyscy liczący się producenci. Osiągnięcia w tym zakresie ma Volvo Construction Equipment, Caterpillar, Komatsu, New Holland, Case, F. Weyhausen oraz Hitachi. Maszyny wyposażone w napęd hybrydowy składający się z silnika spalinowego oraz maszyny elektrycznej (generator synchroniczny), układu energoelektronicznego i wysoko wydajnego akumulatora mogą spalać nawet o 40% mniej paliwa. To imponujący wynik, ale problem jak zwykle w takich przypadkach tkwi w cenie. Potencjalni nabywcy zastanawiają, jak długo muszą eksploatować maszynę, by inwestycja w „hybrydę” zaczęła się zwracać. Widać wyraźnie, że przygotowania wielu producentów do wdrożenia maszyn z napędem hybrydowym do seryjnej produkcji zostały nieco zahamowane przez kryzys ekonomiczny oraz spadek cen ropy naftowej. Problemem pozostaje także bardzo wysoki koszt akumulatorów. Mankamentem są też ich duże gabaryty i waga. Ogranicza to możliwości stosowania napędu hybrydowego w mniejszych maszynach. Konstruktorom New Holland mających duże doświadczenia w budowie maszyn kompaktowych nie udało się skutecznie „upakować” hybrydowego napędu w nadwozie produkowanych seryjnie koparek. Do pełni szczęścia brakuje im ciągle ok. 50 cm, niby niewiele, ale jednak.

Fot. 5. Napęd hybrydowy to przyszłość rozwiązań konstrukcyjnych maszyn budowlanych
Nie dziwi zatem specjalnie, że coraz bardziej słyszalne stają się głosy przeciwników napędu hybrydowego. Mają oni zresztą mocne argumenty. Uważają na przykład, że środki przeznaczane na rozwój drogiej technologii hybrydowej wykorzystać należałoby raczej na poszukiwanie sposobów uruchomienia rezerw tkwiących w tradycyjnych rozwiązaniach konstrukcyjnych. Faktem jest w końcu, że dzisiejsze koparki hydrauliczne wykorzystują efektywnie zaledwie do 30% mocy silnika. Jej znakomita większość jest zatem bezpowrotnie tracona w układach mechanicznym i hydraulicznym. W głównej mierze wynika to z tego, że ich silnik i pompa hydrauliczna pracują w górnym zakresie wydajności, choć do należytego wykonania prac jest to niezbędne jedynie w stosunkowo rzadkich przypadkach. Nie zapominać również należy o wspomnianym już problemie związanym z permanentnymi spadkami ciśnienia w układzie hydraulicznym. Przepływa przezeń stale olej hydrauliczny, nawet wówczas gdy nie jest to niezbędne do wykonania cyklu roboczego. Konstruktorzy nie uporali się także dotychczas z pozoru łatwym do rozwiązania problemem odzyskiwania energii traconej w momencie zatrzymywania w konkretnej pozycji obracającego się nadwozia maszyny. A są to przecież straty oczywiste i – jak do tej pory – bezpowrotne.
Obecnie wiele się dyskutuje na temat zagrożenia globalnym ociepleniem i związanej z nim konieczności ograniczenia emisji dwutlenku węgla. Jeżeli chodzi o maszyny budowlane, to sposobem na to może być stosowanie całkowicie elektrycznego napędu. Jest to zresztą swoisty powrót do przeszłości. Tego rodzaju rozwiązania były stosowane w praktyce. Wystarczy przypomnieć sobie choćby koparki kolosy marki Skoda spotykane do dziś w kopalniach surowców skalnych. Nie cieszą się one jednak uznaniem użytkowników nie tyle ze względu na przestarzałą konstrukcję i słabe parametry pracy, ile małą mobilność. Koparka napędzana silnikiem elektrycznym ma ograniczony zasięg ze względu na doprowadzenie zasilania za pomocą kabla. Po każdorazowym przemieszczeniu maszyny niezbędne jest jego przepinanie, co jest pracochłonne i zabiera mnóstwo czasu. Mankamentem jest także duża podatność kabla na zerwanie i wszelkiego rodzaju uszkodzenia mechaniczne. Grozi to nie tylko porażeniem prądem elektrycznym, ale i bezproduktywnymi przestojami.
Nic zatem dziwnego, że konstruktorzy maszyn budowlanych dążą do całkowitego pozbycia się kabla. Efekty ich prac są zauważalne. Japoński koncern Hitachi oferuje na przykład koparkę BEX (Battery Excavator) napędzaną silnikiem elektrycznym o mocy 32 kW (44 KM). Jest on zasilany bez użycia kabla za pomocą umieszczonych na maszynie akumulatorów litowych. Niewątpliwą zaletą koparki BEX jest nieemitowanie spalin i cicha praca. Moc silnika elektrycznego zastosowanego w maszynie Hitachi porównywalna jest z parametrami spalinowych jednostek napędowych. Producent podaje, że na jednym ładowaniu maszyna przemieścić może nawet do 60 m3 urobku. W przeciętnych warunkach pracy koparka wymaga zatem ładowania co 2–3 godziny. Powodem jest ciągle niezadowalająca pojemność akumulatorów. Istotny problem stanowi też ich wysoka waga oraz duże gabaryty. Akumulatory są też po prostu drogie. Wszystko to oznacza spadek efektywności wykorzystania maszyny. Testy prowadzone w Japonii wykazały co prawda, że „koparka na baterie” pozwala użytkownikowi oszczędzić nawet do 60% na kosztach paliwa. Czy jej zakup i codzienna eksploatacja są jednak naprawdę opłacalne? Szacuje się, że cena maszyny elektrycznej jest o ok. 30% wyższa w porównaniu z tradycyjną konstrukcją. Jednak to tylko jeden aspekt sprawy. Sporym mankamentem zakłócającym rytmiczność prowadzonych robót są częste przestoje konieczne na ładowanie akumulatorów, a trwa ono znacznie dłużej niż tankowanie zwykłej maszyny.
Jacek Barański
Zdjęcia autora