12 września br. w Łochowie podczas Forum Rusztowaniowego – cyklicznej imprezy organizowanej przez Polską Izbę Gospodarczą Rusztowań, ogłoszono wyniki II edycji Konkursu Rusztowanie Roku – konkursu, którego celem jest promowanie nowatorskich rozwiązań projektowych i technologicznych oraz dobrych i bezpiecznych praktyk przy budowie konstrukcji z rusztowań.
Laureaci w kategorii I – Rusztowanie
I miejsce i nagroda Złotego Kuplunga: realizacja tymczasowej hali z konstrukcji rusztowań modułowych na terenie elektrowni Bełchatów wykonana przez firmę Bis plettac.
II miejsce i nagroda Srebrnego Kuplunga: ex aequo rusztowania robocze wiszące na moście w Puławach wykonane przez firmę Ramirent oraz „Latające Rusztowanie” – konstrukcja rusztowania posadowionego na bandażach kotła bloku 858 MW w elektrowni Bełchatów zrealizowane przez firmę ThyssenKrupp Xervon Polska.
III miejsce i nagroda Brązowego Kuplunga: konstrukcja rusztowania wsporczego pod budowę kopuły reaktora Babcock w Stoczni Marynarki Gdańskiej zrealizowana przez firmę Rubo Serwis.

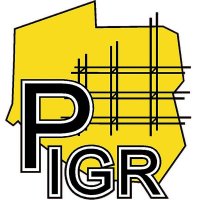
Więcej szczegółów dotyczących konkursu: www.rusztowania-izba.org.pl
Danuta Gawęcka
dyrektor PIGR
Złoty Kuplung
Tę prestiżową nagrodę zdobyła tymczasowa hala z konstrukcji rusztowań modułowych na terenie elektrowni Bełchatów, wykonana przez firmę BIS plettac.
Konstruktorzy i budowniczowie hali musieli zrealizować ważne zadanie. Należało stworzyć obiekt, którego głównym zadaniem była ochrona przed warunkami atmosferycznymi wielkogabarytowych kanałów spalin o przekroju rurowym, wytwarzanych z tworzyw sztucznych na potrzeby Elektrowni Bełchatów. Hala montowana była z typowych elementów stalowych rusztowania: „plettac Perfect Contur”. Wymiary wewnętrzne hali to: 13,0 m x 25,0 m x 14,0 m. W zakresie nietypowości realizowanych prac szczególną uwagę należy zwrócić na wykonanie konstrukcji dachu oraz bramy rozsuwanej. Z uwagi na okres użytkowania hali (również w okresie zimowym) pokrycie dachu zaprojektowano z blachy stalowej trapezowej typu TR18.214. Ze względu na nietypowość pokrycia – jak dla konstrukcji rusztowaniowych – mocowanie blachy z dźwigarami odbyło się za pomocą łat z drewna klasy C18 o przekroju 10 x 5 cm w rozstawie co 0,80 m. Scalenie rusztowaniowych złączy klinowych z łatami drewnianymi zrealizowano poprzez wkręty samogwintujące. W obliczeniach statycznych uwzględniono pełne obciążenie śniegiem (druga strefa zgodnie z PN-80/B-02010/Az1:2006). Sama konstrukcja zadaszenia wykonana została z dźwigarów kratowych o wysokości 0,70 m, stężonych elementami systemowymi rusztowania (wysokość kalenicy dachowej +16,0m).

Fot. Archiwum firmy BIS plettac
Brama rozsuwana zrealizowana została w kształcie dwuskrzydłowych wrót o wymiarach całkowitych 11,0 x 12,5 m, osłoniętych blachą stalową zamocowaną na stelażu z rur kwadratowych 50 x 50 x 4 mm oraz konstrukcji z dźwigarów kratowych. Układ jezdny bramy wykonano z wózków jezdnych, aby sprostać wymogom inwestora, tzn. swobodnie transportować elementy kanału spalin wykonane wewnątrz hali. Obiekt został zaprojektowany w sposób umożliwiający rozsuwanie bramy oraz pozostawianie hali otwartej podczas wiatru o prędkości do 10m/s. Nietypowość sposobu podwieszenia bramy wynikała z tego, że standardowe dźwigary systemowe nie posiadają wystarczającej nośności do podwieszenia tak dużego ciężaru. Zastosowano więc kratową belkę przestrzenną zaprojektowaną z czterech typowych dźwigarów systemowych o wysokości 0,70 m. Układ jezdny bramy pozwalał na rozsuwanie wrót o wymiarach pojedynczego skrzydła: 5,50 m x 12,50 m. W tym celu zastosowano pięciorolkowe wahliwe i regulowane wózki jezdne, po 4 szt. na każde skrzydło bramy. Zostały one zawieszone na profilu 80 x 80 x 5 mm (rura kwadratowa) podwieszonym do dźwigarów stalowych. Dolną część bramy oparto na kołach jezdnych przesuwanych w prowadnicach z ceownika walcowanego. Należy dodać, iż uzupełniającym przedsięwzięciem wykonanym przez Inwestora była realizacja wewnątrz hali płyty fundamentowej oraz torowiska, pozwalających transportować wytwarzane w hali elementy instalacji przemysłowej. Wymiary wrót po ich całkowitym rozwarciu pozwalały wsunąć po torowisku, obiekt o wielkości przeciętnego domku jednorodzinnego.
Kolejnym ważnym elementem innowacyjności montażu było zachowanie stateczności ogólnej obiektu tymczasowego z rusztowania. W tym celu zastosowano balast w postaci żelbetowych płyt drogowych o wymiarach 0,16 x 1,5 x 3,0 m i całkowitym ciężarze około 21,6 ton. Rozmieszczenie płyt było zgodne z geometrią pól rusztowania – umieszczono je pod zewnętrznymi parami stojaków. Połączenie stojaków konstrukcji nośnej z balastem odbyło się dzięki zastosowaniu standardowych kotew rusztowaniowych. Po dokonaniu badania nośności połączeń kotwiących stwierdzono, że siła wyrywająca pojedynczą kotew przekracza 6,0 kN, tj. minimalną wymaganą wartość wyliczoną w projekcie.
Pokrycie ścian hali wykonano z plandeki mocowanej w specjalnych profilach aluminiowych (tzw. profilach kederowych). Dodatkowym elementem komunikacji, oprócz wrót rozsuwanych, było wejście o wymiarach 5,0 x 4,0 m zlokalizowane w drugiej ścianie szczytowej.
Wysoką jakość usług BIS plettac Sp. z o.o. potwierdziło również szybkie tempo wykonania hali, przy zachowaniu bezpieczeństwa montażu. Jako prewencję opracowano dokument określający środki zaradcze obniżające ryzyko, a sama konstrukcja podlega okresowym przeglądom przeprowadzanym przez pracownika nadzoru BIS plettac. Hala, omawiana w powyższym artykule, nie była jedynym obiektem nietypowym wykonanym z rusztowań na opisanej budowie. Różnorodne inne konstrukcje ułatwiały wykonanie całego procesu montażu instalacji kanałów spalin elektrowni (łączenie elementów kanałów oraz przyłącza do chłodni kominowej).
Dodatkowymi referencjami obiektu z rusztowań, oprócz rekomendacji Inwestora (firma Kurotec-Polska Sp. z o.o.) był artykuł pt. „Rusztowania – ciekawe i nietypowe realizacje realizowane w przemyśle” w „Inżynierze budownictwa” nr 11/2008. Tam też opisano pozostałe parametry obiektu oraz specyfikę projektowania konstrukcji tymczasowych z rusztowań.
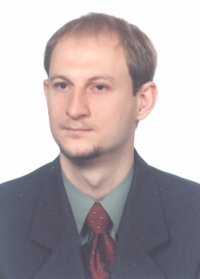
mgr inż. Piotr Kmiecik, projektant hali
Srebrny Kuplung
Rusztowania podwieszane na moście w Puławach.
Budowa mostu im. Jana Pawła II przez Wisłę w ciągu obwodnicy Puław, wraz z trasą objazdową, była największą tego typu inwestycją w kraju. Wiszące rusztowania robocze na moście wykonała firma Ramirent.
Most zbudowany jest w konstrukcji stalowej łukowej z płytą pomostową podwieszoną w dolnym pasie. Przęsło nurtowe mostu posadowione jest na dwóch filarach mostowych odległych od siebie o ok. 200 m. Całkowita długość mostu to ok. 450 mb. Wysokość konstrukcji mierzona od poziomu lustra wody wynosi ok. 50 m. Podczas prac montażowych oraz wykonywania zabezpieczeń antykorozyjnych konstrukcji nośnej mostu wykorzystane zostało rusztowanie podwieszane. Używano je do prac spawalniczych, antykorozyjnych i malarskich. Prace montażowe trwały od kwietnia do czerwca 2008 r.
Prace przygotowawcze
Realizację montażu rusztowań rozpoczęto od określenia: celu i zasadności ustawienia rusztowań, zestawień obciążeń, możliwości wykonania zamocowań i kotwień.
Na ich podstawie wybrano najkorzystniejsze i najbardziej ekonomiczne rozwiązanie. Wybrano rusztowania Layher, łącząc ze sobą dwa systemy: rusztowanie ramowe Blitz o szerokości 0,73 m i długości 2,57 m (rusztowanie to zapewniało komunikację pionową) oraz rusztowanie modułowe AllRound o szerokości stojaków od 0,73 m do 1,09 m i długości pola od 0,73 m do 3,07 m (to rusztowanie pełniło funkcję rusztowania roboczego).
Montaż
Konstrukcja rusztowania została wykonana z systemowych elementów rusztowania modułowego AllRound. Rusztowanie zostało podwieszone na dźwigarach kratowych stalowych ustawionych na górnej powierzchni łuku mostowego. Stojaki rusztowania połączone zostały z górnym i dolnym pasem dźwigara za pomocą złączy krzyżowych. Rygle łączące stojaki stanowiły podparcie dla pomostów roboczych oraz pomostów komunikacyjnych. Tak wykonane ramy, zawieszone z obu stron łukowej belki mostowej, połączone były ze sobą za pomocą U-rygli podwójnych. Stanowiły też podparcie dla pomostu roboczego wykorzystywanego podczas zabezpieczenia dolnej części łuku mostowego. Konstrukcję rusztowania ustawioną na górnych pasach łuku mostowego zabezpieczono przed przesuwaniem za pomocą rur stalowych Ø 48 opartych na cięgnach podtrzymujących płytę pomostową.
Całość konstrukcji została stężona za pomocą systemowych stężeń pionowych zamontowanych z obu stron łuku mostowego. Projekt przewidywał wykorzystanie różnych długości modułów w celu dostosowania do zmiennego nachylenia łuku mostowego zarówno w kierunku podłużnym, jak i poprzecznym. Skutkowało to koniecznością montażu różnych długości pól (2,07−3,07 m) w zależności od nachylenia łuku, stojaków (ze skokiem kryzy co 0,5 m) oraz stężeń pionowych i poziomych.
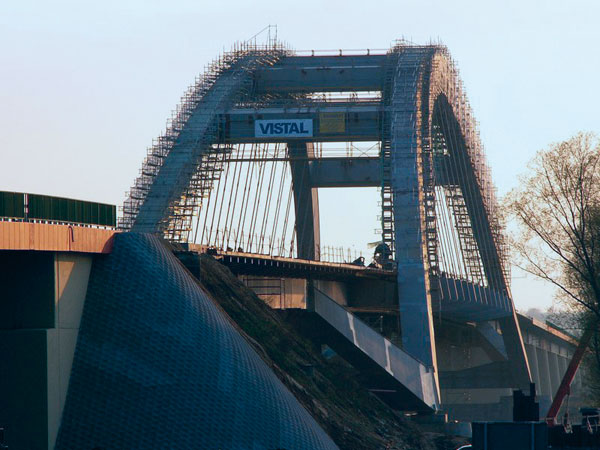
Rusztowania na łukach. Fot. Archiwum firmy Ramirent
Organizacja robót
Dostawy rusztowań realizowano z magazynów regionalnych Ramirent w Podolszynie k. Warszawy i Bytomiu. Inwestycję przy współudziale biura konstrukcyjnego obsługiwał oddział Lublin. Projekt techniczny przewidywał organizację placu budowy z uwzględnieniem całej technologii dostaw sprzętu oraz wykonania montażu i demontażu rusztowań. Sprzęt do transportu pionowego i poziomego oraz tymczasowe ogrodzenia dostarczyła również firma Ramirent.
Do realizacji montażu rusztowań przystąpiono, dostosowując tempo prac do potrzeb zleceniodawcy. W tym samym czasie na placu budowy pracowało pięć grup montażowych złożonych z najbardziej doświadczonych pracowników firmy. Praca na znacznej wysokości, nad wodą i otwarta przestrzeń stwarzały szczególnie niesprzyjające warunki. Dobór monterów z odpowiednimi kwalifikacjami oraz osób nadzorujących z dużym doświadczeniem pozwolił na bezpieczną pracę. Każda grupa montażowa otrzymała niezależny zakres prac, co pozwoliło dokładnie śledzić postępy oraz przekazywać i rozliczać wykonane zakresy montażu. Dodatkowo prace montażowe wspierała grupa logistyczna, odpowiedzialna za dostarczenie rusztowań w miejsce prowadzonych montaży oraz utrzymanie nadzoru nad prawidłowym postępem prac.
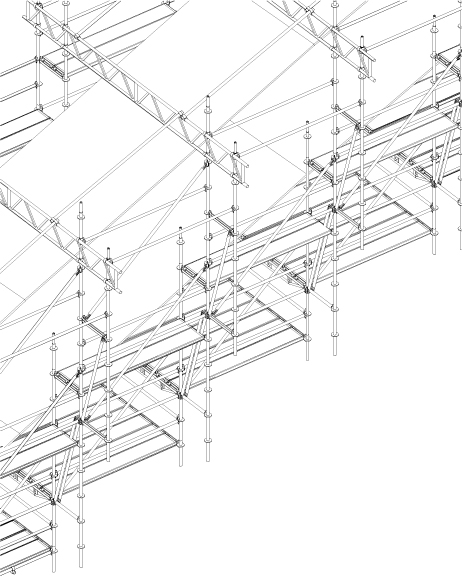
Rys. 1. Całość konstrukcji została stężona za pomocą systemowych rozwiązań
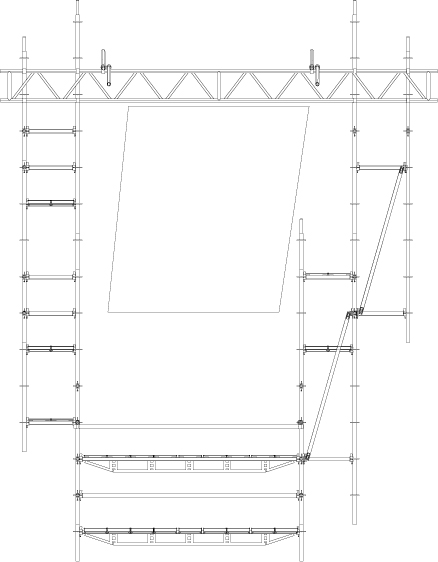
Rys. 2. Konstrukcje rusztowania podwieszanego ustawioną na górnych pasach łuku mostowego
Oddanie mostu do użytku
Realizacja zakończona została w zakładanym terminie. Rozwiązania zastosowane przy tej realizacji weszły na stałe do wybudów systemowych oferowanych przez Ramirent. Nastąpiło oficjalne otwarcie mostu. Kronikę dokumentującą postęp prac przy budowie mostu w Puławach można obejrzeć na www.pulawymost.pl.
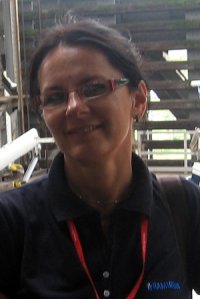
Elżbieta Nowicka-Słowik
Kierownik Produktu Rusztowania Ramirent SA
członek Rady ŚLOIIB
członek Rady ŚLOIIB
Elektrownia Bełchatów – rusztowania dla tzw. bandaży bloku XIII 858 MW
Wkrótce dzięki nowo budowanemu blokowi energetycznemu elektrowni Bełchatów przypadnie tytuł największej elektrowni na świecie wytwarzającej energię elektryczną z węgla brunatnego.
Przy największej elektrowni w Polsce i obecnie jednym z największych placów budowy w kraju funkcjonuje oddział ThyssenKrupp Xervon Polska Sp. z o.o. – przedsiębiorstwa specjalizującego się w budowie skomplikowanych technicznie konstrukcji z rusztowań.
Główny wykonawca inwestycji − konsorcjum Alstom Power Sp. z o.o. i Rafako SA − podpisał z ThyssenKrupp Xervon Polska umowę na wyłączność dostaw rusztowań w obszarze kotła oraz umowy na prace w maszynowni i innych obiektach powstającego bloku na parametry nadkrytyczne o przewidywanej mocy znamionowej 858 MW. Zakres prac ThyssenKrupp Xervon na budowie bloku objął nie tylko rusztowania, ale również pozostałe zabezpieczenia BHP, takie jak plandeki, siatki, podwieszane siatki asekuracyjne itp.
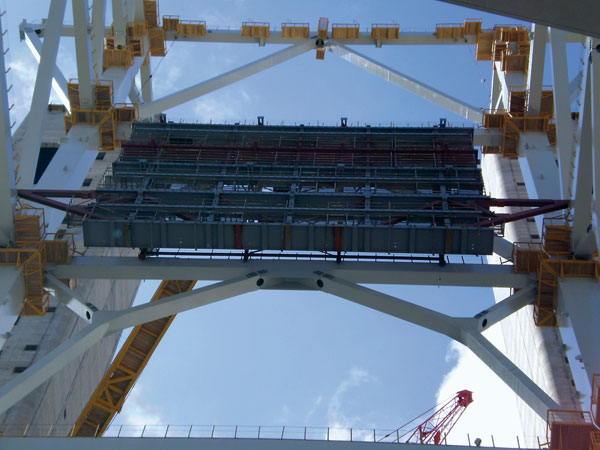
Fot. Archiwum firmy ThyssenKrupp Xervon Polska
Rusztowanie na bandażach kotła
Jednym z wyzwań było wykonanie rusztowania na bandażach kotła. Rusztowanie to miało posiadać cechy rusztowania stacjonarnego i zarazem lekkiego, spełniającego wszystkie wymogi BHP i co najważniejsze wytrzymałego na wszelkie oddziałujące siły zewnętrzne, którym będzie poddane na budowie. Konstrukcja docelowo miała zostać zainstalowana na wysokości od 77,10 m do 127,60 m, co wiązało się z koniecznością transportu całości za pomocą dźwigu.
W pierwszej kolejności przygotowano projekt wykonawczy rusztowań, sporządzony i sprawdzony przez uprawnione do tego osoby. Priorytetem przy jego tworzeniu było zapewnienie maksymalnej sztywności oraz stabilności konstrukcji, dlatego też projektant po dokonaniu niezbędnych wyliczeń statycznych zastosował do wykonania zadania materiał systemu Modex i jego moduły o wymiarach 2,5 m x 1,13 m i 2,5 m x 0,82 m; 1,13 m x 2,0 m; 1,13 m x 3,0 m i 1,13 m x 4,0 m.
Modułowy system Modex, mający świadectwo dopuszczenia do użytkowania przez Niemiecki Instytut Techniki Budowlanej w Berlinie, cechuje się dużą elastycznością zastosowania. Głównym jego elementem, pozwalającym na budowę konstrukcji w górę, są nośne elementy pionowe powszechnie nazywane choinkami lub prętami. Elementy te to stalowe rury ø 48,3 mm długości od 1 do 4 m, posiadające co 50 cm węzły, w które można zapinać kolejne elementy. Węzły te umożliwiają przyłączenie do 8 elementów usytuowanych zarówno w poziomie, jak i biegnących ukośnie, a obciążenia, jakie mogą wytrzymać, wynoszą odpowiednio:
– siła normalna = ±16 kN
– siła poprzeczna (pionowa) maks. na węzeł = 48 kN
– siła poprzeczna (pozioma) = ±17 kN
– moment gnący = ±47 kNcm
– siła osiowa = ±9 kN
Natomiast obciążenie użytkowe dla pomostów roboczych uzależnione jest od długości modułu oraz sposobu podparcia i wynosi od 2 do 6 kN/m2. Przy optymalizacji parametrów konstrukcji rusztowania z Modexu można budować nawet do 58 m wysokości bez dodatkowych przeliczeń statycznych. Parametry stali, z której elementy systemu zostały wykonane, posiadają zgodności z wszelkimi normami dopuszczającymi je do użytkowania w Polsce.
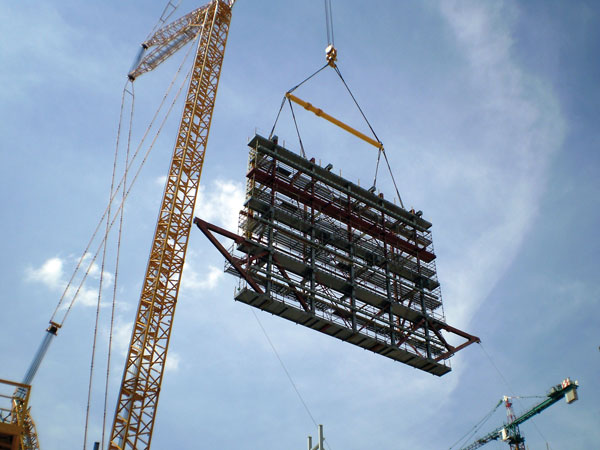
Fot. Archiwum firmy ThyssenKrupp Xervon Polska
Jednak sam system Modex nie eliminuje wszystkich problemów powstających przy konstrukcji rusztowań nietypowych. Największą trudność projektu rusztowania na bandażach kotła stanowiło zapewnienie sztywności całej konstrukcji oraz zakotwienie, które nie pozwoliłoby na jakiekolwiek przesunięcie podczas transportu na wysokość ponad 77 m. Dodatkowo ograniczona nośność dźwigu transportującego całość konstrukcji na miejsce instalacji przy kotle oraz ograniczenia wynikające z wytrzymałości nośności słupów kotła wymuszały maksymalne zmniejszenie ciężaru rusztowania przy zachowaniu wszystkich zabezpieczeń BHP. Istotnym elementem, który uwzględniono, były siły wiatru, które nie tylko utrudniały pracę dźwigu, ale również stwarzały ryzyko destabilizacji konstrukcji rusztowaniowej. Należało również przewidzieć bezpieczną technikę demontażu rusztowania. Na wysokości 77–120 m stanowiło to duże wyzwanie, gdyż cały proces musiał być przeprowadzony szybko i efektywnie, nie uszkadzając przy tym konstrukcji kotła i nie powodując strat w materiale.
Mając na uwadze powyższe trudności, ThyssenKrupp Xervon opracowała wstępny projekt techniczny, w którym zaproponowała rozwiązanie konstrukcji rusztowaniowej, uwzględniając nieodzowne jej cechy, tj.: wytrzymałość, odpowiednią sztywność, lekkość oraz bezpieczeństwo. Ponadto ze względu na brak możliwości ingerencji w czasie transportu rusztowanie musiało zostać zabezpieczone przed przesunięciem i upadkiem z wysokości, a jego poszczególne elementy, mimo iż nie przytwierdzone na stałe, nie mogły odpaść od całości konstrukcji.
Po zatwierdzeniu przez inwestora ogólnej koncepcji rusztowań i technologii montażu zdecydowano się na rozpoczęcie prac. Na każdym etapie realizacji tego przedsięwzięcia w stan gotowości były postawione wszystkie służby realizacyjne, złożone z pracowników działu „inżynieringu”, logistyki, nadzoru technicznego, wewnętrznych służb BHP oraz ekip monterów i specjalistycznych grup alpinistycznych. Wszyscy uczestnicy projektu posiadali wymagane przez polskie prawo uprawnienia, szkolenia BHP oraz niezbędne badania lekarskie konieczne do wykonywania powierzonych im zadań.
Do dziś cały projekt nie został jeszcze wykonany w 100 procentach, przed ThyssenKrupp Xervon stoi kolejne wyzwanie, jakim jest proces demontażu, równie ważny i wymagający profesjonalnego podejścia wszystkich pracowników.

mgr inż. Mirosław Sokołowski
Dyrektor ds. Realizacji i Marketingu
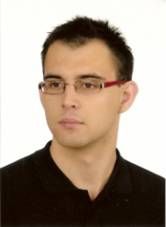
mgr Kamil Migdał
Doradca ds. Handlowych
Zdobywcę Brązowego Kuplunga − realizację rusztowań pod budowę kopuły reaktora atomowego przez firmę Rubo-Serwis − przedstawimy w listopadowym numerze „IB”.