W Bytomiu na placu Kościuszki powstaje wielofunkcyjna galeria Agora Bytom. Ze względu na umiejscowienie obiektu wśród zwartej zabudowy miejskiej, i zaprojektowane kondygnacje podziemne zastosowano zabezpieczenie wykopu w postaci ścian szczelinowych.
Galerię zaprojektowało Biuro Projektowo-Doradcze Arkus z Gliwic oraz Biuro Inżynieryjno-Konsultingowe Niras Polska Sp. z o.o. Inwestorem jest firma Braaten+Pedersen plus Partners. Wykorzystanie ścian szczelinowych pozwoliło na zminimalizowanie wpływu wykopu na sąsiadującą zabytkową zabudowę, a także na odcięcie dopływu wody gruntowej do wykopu, dzięki czemu nie będzie konieczne odwadnianie gruntu wokół budowy, które mogłoby spowodować osiadania otaczającego terenu.
Niżej omówiono technologię realizacji ścian szczelinowych z wykorzystaniem systemu ciągłego złącza wodoszczelnego CWS® firmy Soletanche Polska na przykładzie skomplikowanej logistycznie budowy, gdzie zaprojektowano ścianę szczelinową grubości 60 i 80 cm, słupopale tymczasowe oraz ścianę środkową oddzielającą sąsiednie segmenty budynku różniące się liczbą kondygnacji podziemnych. Ściana szczelinowa, która w fazie tymczasowej stanowi obudowę i zabezpieczenie stateczności wykopu, w fazie docelowej będzie stanowić ścianę zewnętrzną kondygnacji podziemnych.
Galerię Agora zaprojektowano na rzucie zbliżonym do prostokąta o wymiarach około 163,0 x 73,0 m. Budynek podzielono na trzy segmenty, przy czym segment pierwszy posiada dwie kondygnacje podziemne (maks. głębokość wykopu –12,93 m poniżej 0 budynku), a segmenty drugi i trzeci jedną kondygnację podziemną (maks. głębokość wykopu –7,43 m poniżej 0 budynku). Segment pierwszy został oddzielony od segmentów drugiego i trzeciego środkową ścianą szczelinową grubości 80 cm.

Fot. 1. Wiercenie słupopali
Jako metodę stabilizacji ścian szczelinowych w fazie tymczasowej stosuje się różne systemy zapewnienia stateczności ścian (rozpory stalowe, kotwie gruntowe czy stropy wykonane na gruncie i tymczasowo podparte). Sposób zapewnienia stateczności jest dobierany do każdej budowy indywidualnie ze względu na dużą liczbę czynników, które należy uwzględnić, m.in. geometrię ścian, głębokość wykopu, warunki gruntowe, obciążenia zewnętrzne, infrastrukturę podziemną.
Segment pierwszy ze względu na dużą głębokość wykopu został otoczony ścianą szczelinową grubości 80 cm rozpartą stropem pośrednim w poziomie kondygnacji -1, podpartym słupami stalowymi umieszczonymi w palach o średnicy 80 cm.
Wykop dla wykonania płyty fundamentowej segmentów drugiego i trzeciego jest zabezpieczony ścianą szczelinową o grubości 60 cm rozpieraną w poziomie oczepu żelbetowego ściany szczelinowej rozporami stalowymi narożnymi oraz zastrzałowymi pomiędzy oczepem ściany szczelinowej a wykonanym wcześniej środkowym fragmentem płyty fundamentowej.

Rys. 1. Rzut ściany szczelinowej wraz z tymczasowym rozparciem
Warunki gruntowe
Podłoże na terenie działki charakteryzuje się dużą niejednorodnością gruntów. Pod warstwą gruntów nasypowych niebudowlanych, złożonych z luźno ułożonych materiałów powstałych z wyburzenia starych budynków o miąższości do 5,0 m, występuje skomplikowany układ przestrzenny warstw piasków od drobnych po grube, pyłów od miękkoplastycznych po twardoplastyczne oraz glin pylastych i piaszczystych również o różnym stopniu plastyczności. Według dokumentacji geologicznej strop warstwy nieprzepuszczalnej znajduje się od 15 do 24 m poniżej poziomu terenu. Zwierciadło wody gruntowej częściowo napięte stabilizuje się powyżej poziomu posadowienia budynku zarówno w części głębokiej, jak i płytszej. Z tego względu ściany szczelinowe zaprojektowano z zagłębieniem minimum 2 m w warstwie nieprzepuszczalnej (zgodnie z opracowaniem dr. hab. inż. Jacka Pieczyraka) w celu odcięcia dopływu wody gruntowej do wykopu. Ze względu na możliwe wystąpienie różnic pomiędzy dokumentacją geotechniczną a układem warstw w terenie, oraz ze względu na dużą odległość pomiędzy otworami badawczymi w czasie głębienia sekcji pod nadzorem doświadczonego geologa należało potwierdzić osiągnięcie minimalnego zagłębienia w warstwie nieprzepuszczalnej. Głębokość ściany można było na bieżąco modyfikować, tak aby uzyskać zapewnienie spełnienia założeń.
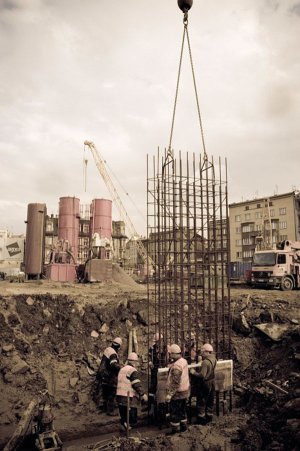
Fot. 2. Instalacja kosza zbrojeniowego w sekcji ściany szczelinowej
Założenia
– Obwód ścian szczelinowych grubości 80 cm – 272 m.b.
– Obwód ścian szczelinowych grubości 60 cm – 238,5 m.b.
– Głębokość ścian dla segmentu 1 – średnio 21,5–26 m poniżej 0 budynku.
– Głębokość ścian dla segmentów 2 i 3 – średnio 18 m poniżej 0 budynku.
– Liczba pali pod słupy tymczasowe – 31 szt. Ø 80 l = 7,5 m słup HEB300.
Ściany szczelinowe to konstrukcje żelbetowe powstałe w wyniku zabetonowania wykopanej w gruncie szczeliny, do której uprzednio wprowadzano zbrojenie. Wykop wykonywany jest w osłonie zawiesiny bentonitowej, zabezpieczającej jego stabilność do czasu betonowania. Betonowanie odbywa się metodą contractor (podwodną) za pomocą kilku rur.
W pierwszej kolejności wykonuje się murki prowadzące ścian szczelinowych o szerokości 64 cm dla ściany 60 cm oraz 84 cm dla ściany 80 cm umożliwiającej swobodne wprowadzenie urządzenia głębiącego.
Następnie w osłonie zawiesiny bentonitowej wykonywany jest wykop jednej sekcji ściany szczelinowej. Długość sekcji wynosi od 2,80 m (długość pojedynczego zbioru chwytaka) do maksimum 9,5 m (długość maks. zależy od parametrów występujących gruntów oraz dodatkowych obciążeń występujących za ścianą szczelinową). Po wykonaniu wykopu zawiesina w szczelinie jest odpiaszczana, a następnie za pomocą dźwigu opuszczane są poszczególne kosze zbrojeniowe. Po wprowadzeniu koszy następuje betonowanie sekcji ściany szczelinowej metodą contractor.
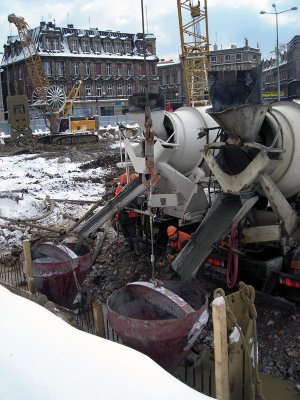
Fot. 3. Betonowanie sekcji ściany szczelinowej
Bezpośrednio po wykonaniu wszystkich sekcji ściany szczelinowej wykonany został oczep żelbetowy spinający wierzch ściany. Po wykonaniu ściany wykonano pale fundamentowe z umieszczonymi słupami stalowymi służące jako podparcie stropu rozpierającego dla segmentu pierwszego.
Dalsze fazowanie prac dla segmentu pierwszego:
– wykonanie wykopu do poziomu pod strop nad -2;
– wykonanie obręczy stropu rozpierającego oraz montaż rozpór stalowych w miejscu otworów technologicznych;
– wykonanie wykopu do poziomu docelowego maks. 12,97 m poniżej poziomu 0 budynku;
– wykonanie płyty fundamentowej;
– wykonanie dalszej konstrukcji podziemnej budynku z uzupełnieniem stropu nad -2 oraz fazowanym usunięciem rozpór stalowych.
Dalsze fazowanie prac dla segmentu drugiego i trzeciego:
– wykonanie wykopu w części centralnej budynku z pozostawieniem odpowiednich przypór ziemnych zabezpieczających stateczność ściany szczelinowej;
– montaż rozpór narożnych oraz wiercenie i sprężenie tymczasowych kotwi gruntowych;
– wykonanie wykopu docelowego do rzędnej maks. 7,43 m poniżej poziomu 0 budynku;
– wykonanie płyty fundamentowej;
– fazowany demontaż rozpór stalowych wraz z wykonywaniem dalszej konstrukcji budynku;
– odcięcie kotwi gruntowych po wykonaniu konstrukcji 0 budynku.

Rys. 2. Przekroje typowe dla segmentu 1 oraz segmentu 2 i 3
Dla segmentów drugiego i trzeciego przygotowano projekt rozpór zastrzałowych pomiędzy oczepem ściany szczelinowej a płytą fundamentową. Równocześnie zamiennie przygotowano projekt kotwienia ściany szczelinowej i po uzyskaniu zgody właścicieli sąsiednich działek wykonano kotwienie. Pozwoliło to na przyśpieszenie robót ziemnych ze względu na brak konieczności fazowania prac z pozostawieniem skarp przy ścianie szczelinowej.
Przy tak dużej inwestycji o zmiennej liczbie kondygnacji podziemnych konieczne było zastosowanie zróżnicowania grubości ścian szczelinowych oraz sposobu ich rozparcia. Dzięki temu uzyskano optymalne rozwiązanie pozwalające wykonać część podziemną budynku w sposób jak najbardziej ekonomiczny i szybki.
Ściany szczelinowe i słupopale zostały zakończone w marcu 2009 r. Obecnie trwają roboty stanu zero i stanu surowego budynku.
Projektantem ścian szczelinowych jest mgr inż. Urszula Tomczak (Soletanche Polska Sp. z o.o.), a kierownikiem budowy na czas wykonania ścian szczelinowych – mgr inż. Krzysztof Graf z tej samej firmy. Roboty w zakresie ścian szczelinowych wykonała firma Soletanche Polska.
mgr inż. Krzysztof Graf
mgr inż. Urszula Tomczak
Zdjęcia: Archiwum firmy Soletanche Polska